From Blueprint to Reality: Demo A and the Road to Implementation
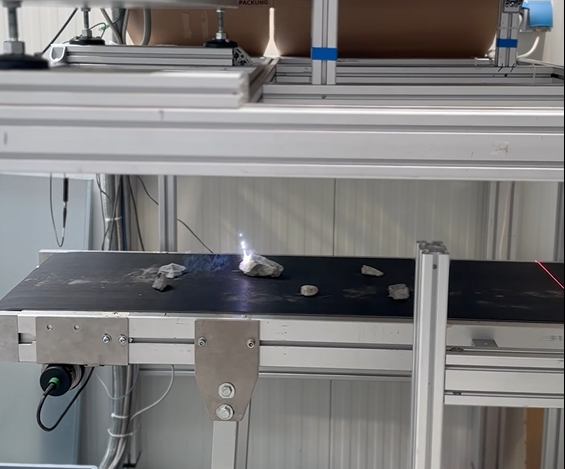
Having passed M24, it is a significant relief that the defined milestones have been achieved on time. Meanwhile, all work packages and many tasks within them have been initiated, leading to a tremendous acceleration in technical progress. As the technical coordinator, it is satisfying to witness such substantial work accomplished. However, it also means that I can no longer dive into every detail. Fortunately, I can rely on a great team, both external and internal, ensuring I receive the most relevant information to maintain a full focus on the bigger picture — bringing the world’s most advanced automated sorting equipment for spent refractories to life.
This milestone will soon be a reality with the completion of the construction and subsequent validation of Demo A, set to happen this year. While significant developments have occurred across various process units, the ultimate test will be the system’s machine performance, primarily reflected in its throughput when all units are integrated. It is crucial to identify the bottleneck in the system. Although we do not anticipate major issues with any unit, even minor discrepancies, like a unit operating at 92% instead of 95% efficiency, can have substantial economic impacts. Therefore, the next few months will be dedicated to several key steps, which we will update in our blog.
Here’s a simplified illustration of the steps we will focus on:
1. Performance of the Singularization Units: Ensuring all particles are well separated to be individually recognized by the system and handled without interference by robots or ejection mechanisms. With the singularization units ready, including the bunker, vibration feeder, and two conveyor belts, a parameter study will commence soon.
Figure 1. Exemplary top view on the conveyor belt after singularization, showing a satisfying result (left) and problematic grouping of particles (right).
2. Correct Classification of Particles: With the main sensor setups in place, we will closely examine particle classification. Initially, broad specifications for sorting classes will be defined, and then these will be refined to their limits
3. Gripping Performance of the Robots and Air Ejection Accuracy: Investigating the mechanical ejection process to ensure particles do not slip from the gripper or show a deviating particle trajectory, not landing correctly in their designated bins.
Figure 2. Picker robot gripping a particle. Images obtained at pilot trials at GeMMe Liège.
These trials will allow us to quantify throughput and calculate process economics, revealing areas needing further development and assessing the robustness of individual units. While there is a lot of work ahead, it is the kind of work that engineers and researchers genuinely enjoy. Stay tuned for our upcoming blog posts where we will delve into each of these steps in more detail.
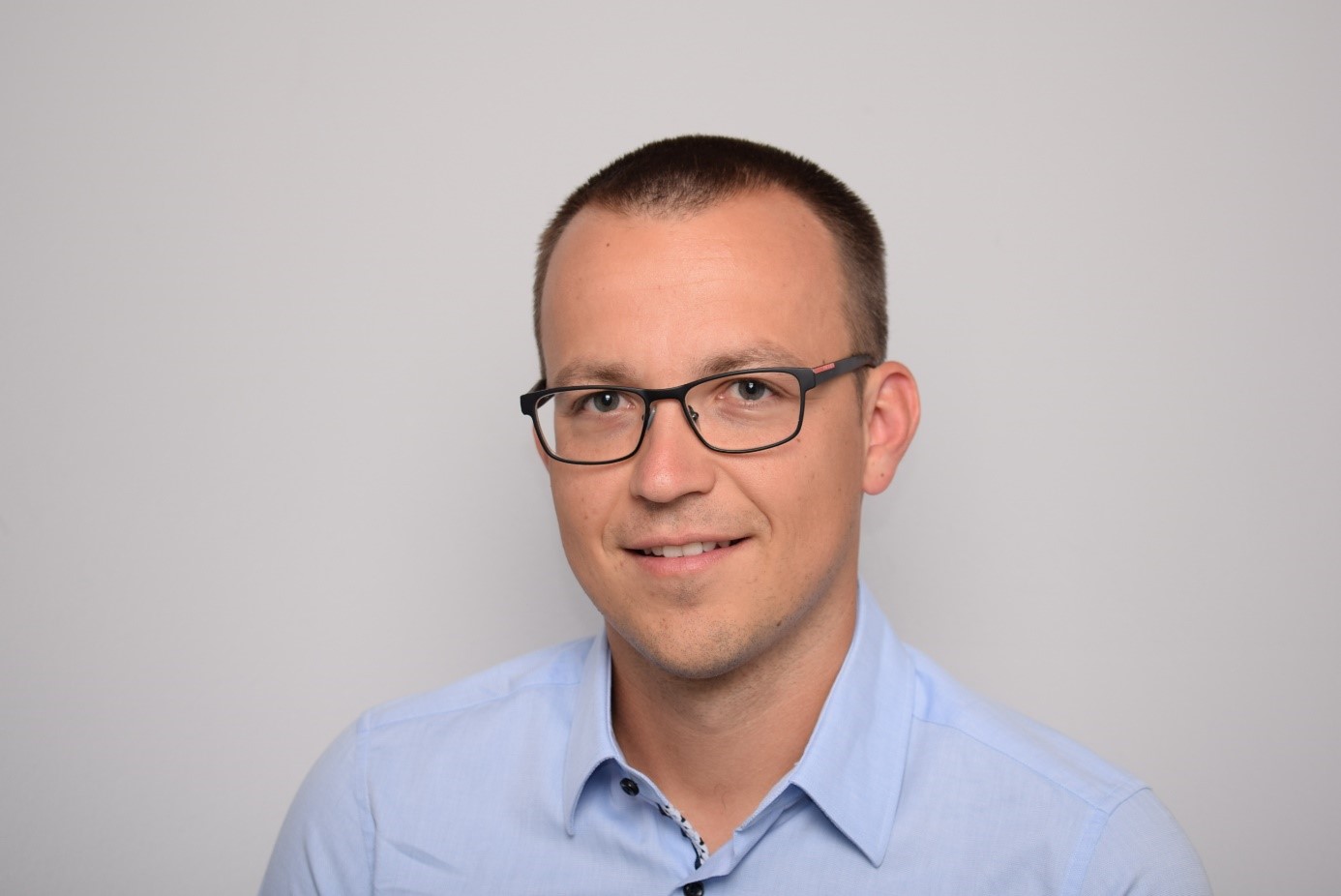
Authors’ Portrait
Alexander Leitner
Alexander studied Material Science at the Montanuniveristät Leoben, focusing on the field of micromechanics and material physics. He joined RHI Magnesita’s Strategic Project and Innovation Team in 2019 and recently joined the business unit Recycling in the field of Recycling Innovation and Technology.
Partner
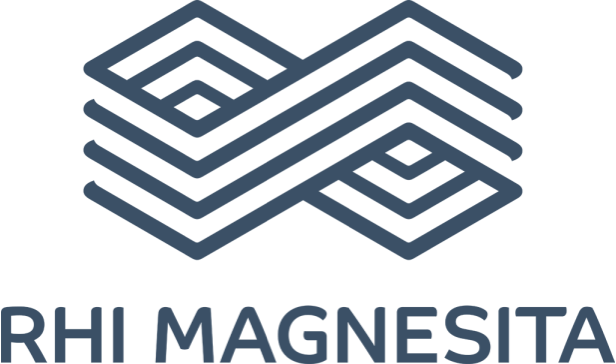