From Code to Action: Behind the Scenes of Connecting Software, Sensors, and Subsystems
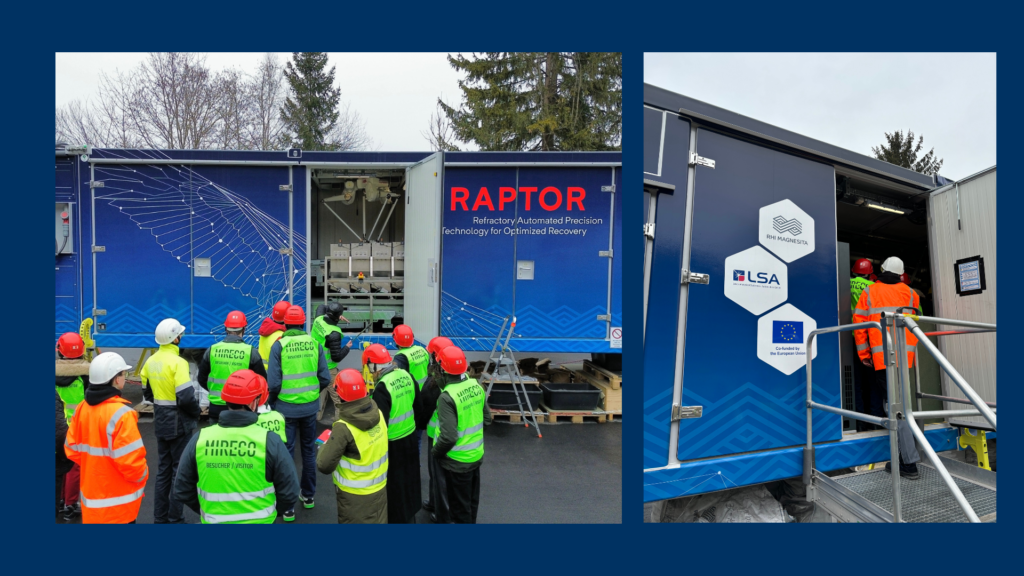
Recently, I had the opportunity to work on a significant task in Mitterdorf, where I was aiming at integrating Fraunhofer ILT’s software into the Demo A machine. This machine represents the culmination of many months of hard work by ReSoURCE’s project members, and it was highly anticipated by those attending a crucial review meeting at RHI Magnesita’s headquarters in Vienna, most of whom had not seen the machine before and had planned to visit the site after the main gathering.
As I arrived in Mitterdorf, the atmosphere was charged with excitement and a bit of pressure. My primary responsibility was to ensure that our software communicated flawlessly with all of the machine’s sensors and other subsystems. Our software’s task is to combine data from various sensors, including NEO’s hyperspectral cameras, the 3D geometry camera, and Innolas’ LIBS laser. From that we classify the bricks and output sorting decisions to the robots and the air ejection unit. Additionally, I needed to replace a crucial component – the line laser for the 3D geometry system – since the old one had failed just a few days before the review meeting. Replacing the line laser also meant recalibrating the entire 3D geometry system. With the project members in Vienna eager to see the machine in action, I focused on making every moment count.
However, the journey was not without its challenges. Developing the software before my trip to Mitterdorf was particularly demanding. Each line of code I wrote felt like a leap of faith, as I couldn’t test it live until I was on-site. The air ejection unit, in particular, proved to be tricky to control, requiring careful attention and problem-solving.
I was fortunate to have tremendous support from my remote team, which made a significant difference. The collaboration with LSA, who provided both remote and on-site assistance, was invaluable. Their expertise and investment in the project were crucial, especially since they assembled the entire Demo A machine. RHI Magnesita also played a critical role, offering us the facilities and samples we needed to move forward. Before my trip to Mitterdorf, we tried to set up as much as possible, but it was evident that some tests could only be done once I was physically present with the machine.
The machine itself is housed in a temperature-controlled container, which allows it to operate effectively in colder conditions. However, this setup posed another challenge. With some of the machine’s access doors needing to be open to fulfil our tasks, the frigid temperatures caused certain components to refuse operation. We had to strategize our schedule carefully, allowing the machine parts time to warm up for testing.
Finally, after what felt like a never-ending chain of troubleshooting and fine-tuning, we succeeded in getting everything operational just a few hours before the review group arrived. I felt a rush of relief as we tidied up the workspace and prepared our presentation, ensuring that all safety measures were in place, especially since we are dealing with powerful lasers that require careful handling. When the group of visitors arrived, the system operated as intended and we were able to show the individual processes and components to the interested project partners.
While I was busy preparing the machine and missed the review meeting part in Vienna, I was aware that my efforts contributed to the project’s success. It was rewarding to know that I played a part in this significant achievement. This experience taught me valuable lessons about teamwork, time management, and adapting to unexpected challenges. It reinforced the importance of collaboration and preparation in navigating complex projects.
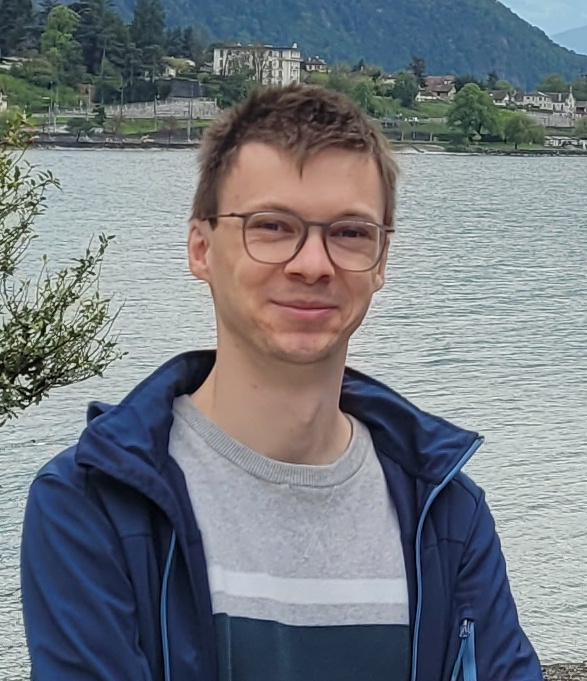
Authors’ Portrait
Yannick Conin
Yannick Conin is a research associate at the Fraunhofer Institute for Laser Technology ILT. He graduated from RWTH University with a master’s degree in mechanical engineering, where he wrote his thesis on sensor fusion for the ReSoURCE project. His research interests include data science, metrology, optics and materials science.
Partner
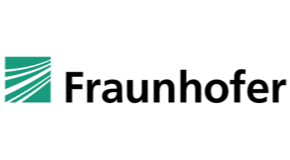