Powder classification experiments at SINTEF
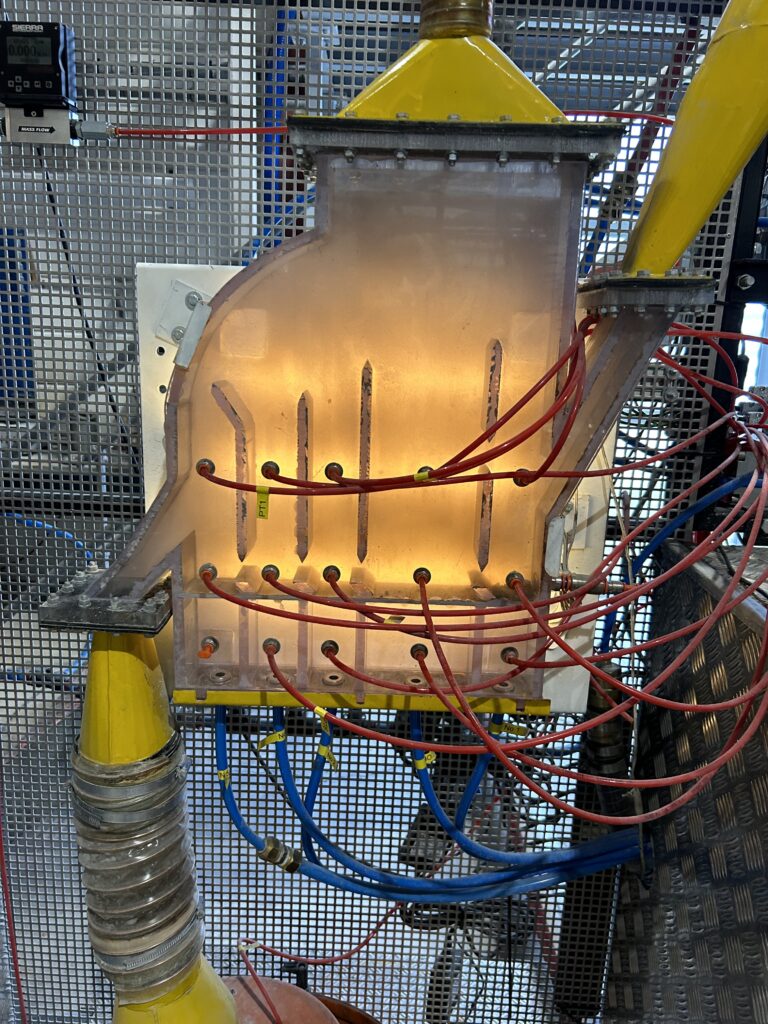
When a furnace, ladle, or kiln lining reaches the end of its service life, the entire lining is extracted with the aid of heavy machinery, necessitating a robust and somewhat aggressive handling process. This break-out procedure results in generation of fine powders, in which bricks and other refractory products are crushed and mingled with impurities from both the service product and its surroundings. Today, most of this fine fraction typically ends up in landfills.
In our ReSoURCE project, we are actively working on the development of a direct sorting method to maximize the recovery of this material for recycling purposes, primarily as refractory material or for further “downcycling” where recycling is infeasible.
The leftover material consists of particles smaller than 5 mm, with the smallest particle sizes qualifying as dust, which poses considerable challenges in terms of material handling. While there exist several techniques for separating particles based on their size and density, it is critical that the chosen method aligns with the composition of the raw material and the desired product fractions. The refractory leftover material presents a complex blend of particles encompassing a wide range of sizes, refractory products, and impurities. Thus, experimental testing to ascertain the efficacy of the method and to optimize the separation process is crucial.
At SINTEF, we are well-equipped to conduct comprehensive testing on the separation, transportation, and handling of powders, from the lab-scale even up to the pilot scale. Initial characterizations of the leftover materials have already shown good fluidization properties within the smallest fractions, measuring less than 1 mm. Experiments using the multi-chamber fluidization classifier (a test rig developed by SINTEF Tel-Tek, former Tel-Tek) has been used to explore the potential for utilizing this technique both for dedusting and as a purification step. The image below illustrates how dust and lighter particles are carried upward within the air stream, while the coarser and heavier particles are transported horizontally and collected separately.
To further enhance the efficacy of the separation process, SINTEF with help from consortium partners have conducted detailed analyses of the particle size distribution and chemical composition of both the fine and coarse fractions. Evaluating the analysis will help us optimizing the separation process towards a cleaner leftover fraction where recycling can be possible.
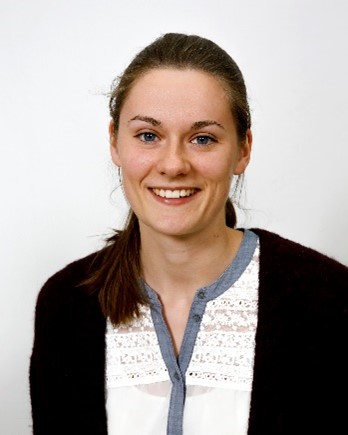
Author’s Portrait
Kristin Søiland
Kristin Søiland is a research scientist at SINTEF Industry in Norway. She has a master’s degree in chemical engineering from the Norwegian University of Science and Technology, specialised in analytical chemistry. At SINTEF her main research areas are within circular economy and powder technology. Prior joining SINTEF she worked in a paint company developing more environmentally friendly coatings.
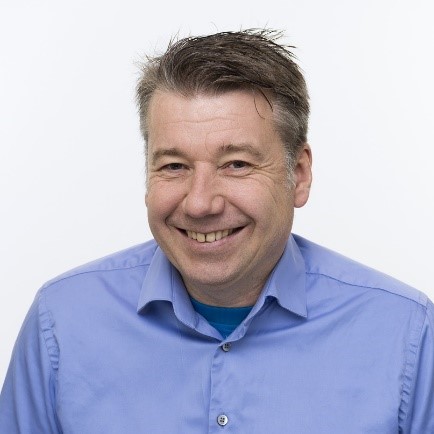
Author’s Portrait
Franz Otto von Hafenbrädl
Franz Otto von Hafenbrädl is a research scientist at SINTEF Industry in Norway. He has several years of experience in powder technology and powder characterization. He started to work with powders in 1996 in Tel-Tek, that is now part of SINTEF. He has a master’s in science of process engineering and a bachelor’s in chemistry from University of South-Eastern Norway.
Partner
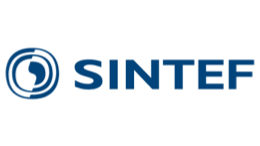