A critical Deliverable
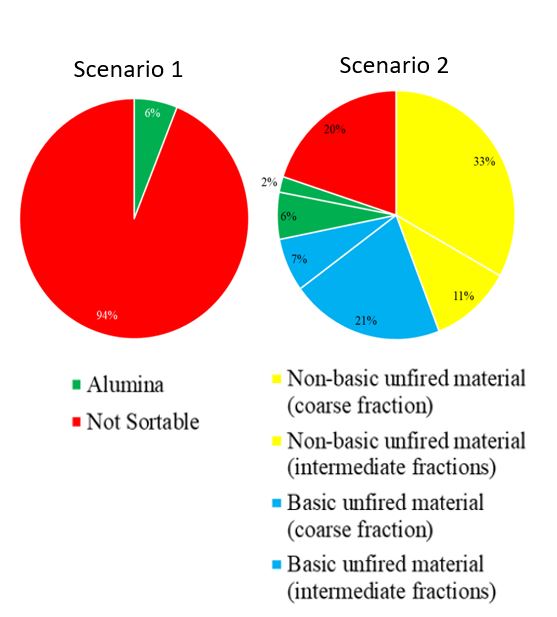
As the project leader of the ReSoURCE team, I am thrilled to let you know that we have submitted our 4th deliverable one day ahead of the deadline. This deliverable is critical to our project, as it contains precise material specifications and internal process information that cannot be shared with the public. However, there are a few non-confidential elements that I would like to share with you.
One of the most crucial aspects of this deliverable is our process for collecting samples of feedstock piles that are as high as 200 tons while ensuring that the samples are still representative. Imagine you’re a gardener and you want to test the soil quality in your garden. You have a large garden with different types of soil and plants growing in different areas. To get an accurate picture of the soil quality, you need to take samples from different parts of the garden. You wouldn’t want to just take a sample from one small area and assume that it represents the whole garden.
Similarly, in our project, we needed to take representative samples of the feedstock piles to get an accurate picture of the material properties. Just like a gardener needs to take samples from different parts of the garden, we needed to take samples from different areas of the feedstock piles to ensure they were representative of the entire batch.
After collecting the samples, we had to determine who would need which type of samples and how much at which time. Let me use another parable here: It’s like organizing a dinner party – you want to make sure you have enough food for everyone, but you don’t want to have too much left over. In the end, we ended up with more than 60 individual sample sets with a total sample weight of 9500kg, which is quite different from what you would expect in a typical lab study.
But that’s not all – we also had to review the currently existing sorting classes of the spent refractories, which we use for manually sorted material. This review made it clear that the classification is not directly based on the chemistry but on secondary properties, such as color or certain material patterns that are visually recognizable. This means that there can be significant overlap between the chemical specifications of different sorting classes, and we had to be aware of that as we moved forward with our project.
Now, let’s talk about the benefits of our automated sensor-based sorting compared to manual sorting. We used a theoretical case example for a specific steel casting ladle to demonstrate this. In one scenario, we used the currently existing approach for manual sorting, and in the other scenario, we implemented the automated sensor-based sorting. The results were striking – in the manual sorting scenario, 94% of the total breakout material was lost for reuse in refractory products and ended up being either a metallurgical additive or landfill. In contrast, in the automated sorting scenario, the proportion of the presently “unsortable” material was significantly reduced to 20% of the total breakout material.
So, what’s next for the ReSoURCE team? We are eager to continue our work and push the boundaries of what’s possible. Stay tuned for more updates on our exciting journey towards a more sustainable future.
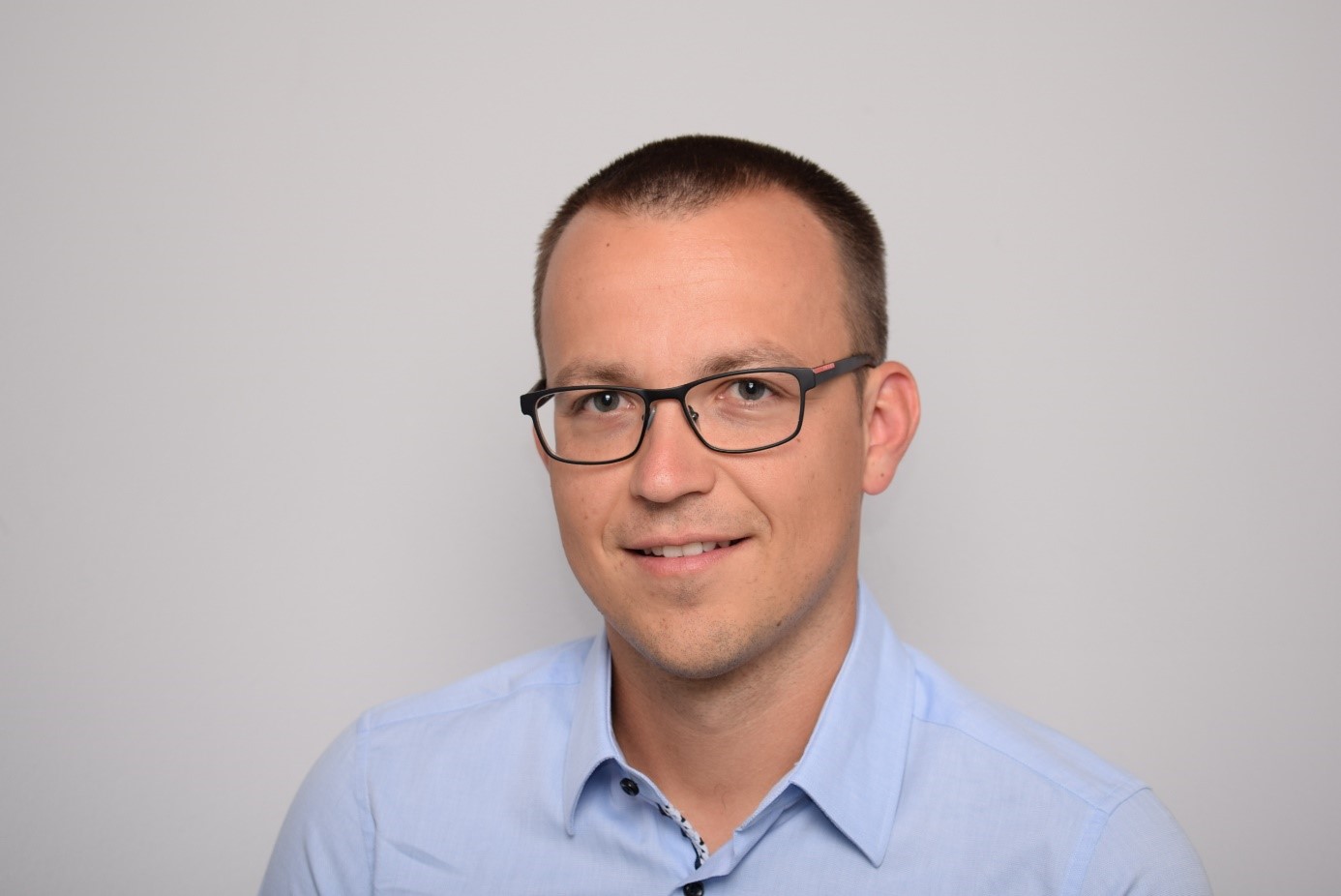
Author’s Portrait
Alexander Leitner
Dr. Alexander Leitner studied Material Science at the Montanuniveristät Leoben, focussing on the field of micromechanics and material physics. He joined RHI Magnesita’s Strategic Project and Innovation Team in 2019 and recently joined the business unit Recycling in the field of Recycling Innovation and Technology.